SAN DIEGO — Aircraft carrier manufacturer Newport News Shipbuilding is revamping its processes to become more efficient as it builds the Gerald R. Ford class of carriers, a company official said.
Brian Fields, the vice president of aircraft carrier construction for CVN-80 and CVN-81, told reporters Feb. 18 the company had a plan going into construction on the Gerald R. Ford, but lessons learned are driving down cost and schedule as the company works through the John F. Kennedy and now the Enterprise.
One lesson relates to crane lifts of large modules or supermodules. Given the immense size of aircraft carriers, the workforce builds the steel framing for segments of the ship, which can then be outfitted with pipes and cables. These modules are then lifted by crane and put into place on the hull.
Fields said the company has learned to use even larger supermodules, therefore needing fewer crane lifts to put the pieces into place.
“Some of our super lifts [on Enterprise] have incorporated what on [Ford and Kennedy] were in some cases 10, 15 erections with a crane — building one large supermodule,” he said. “We’re seeing a lot more opportunity to outfit earlier in the build process, which provides a lot of efficiencies just based on where the work is being performed.”
Fields said the company is also trying to group steel structures into “unit families,” where the pieces aren’t identical but similar enough that lessons can still be applied from one piece to the next. The sequencing on Ford and Kennedy had been based on what steel pieces were needed in what order to form modules that could be stacked in the right order. The new changes on Enterprise mean some steel pieces are built early to need — but Fields said “localized learning” could happen when similar pieces were built consecutively in a “batch manufacturing process.”
Fields said the company is seeing similar learning happening at its 2,500 suppliers around the country.
But, he noted, a driver of the suppliers’ learning is the stability that comes from the Navy’s two-carrier buy of Enterprise and the Doris Miller in 2019. Fields said Newport News Shipbuilding and the Navy were in talks about how to buy and fund aircraft carriers in the future to maintain this optimal construction schedule and industrial base hull-over-hull learning created from the two-ship contract.
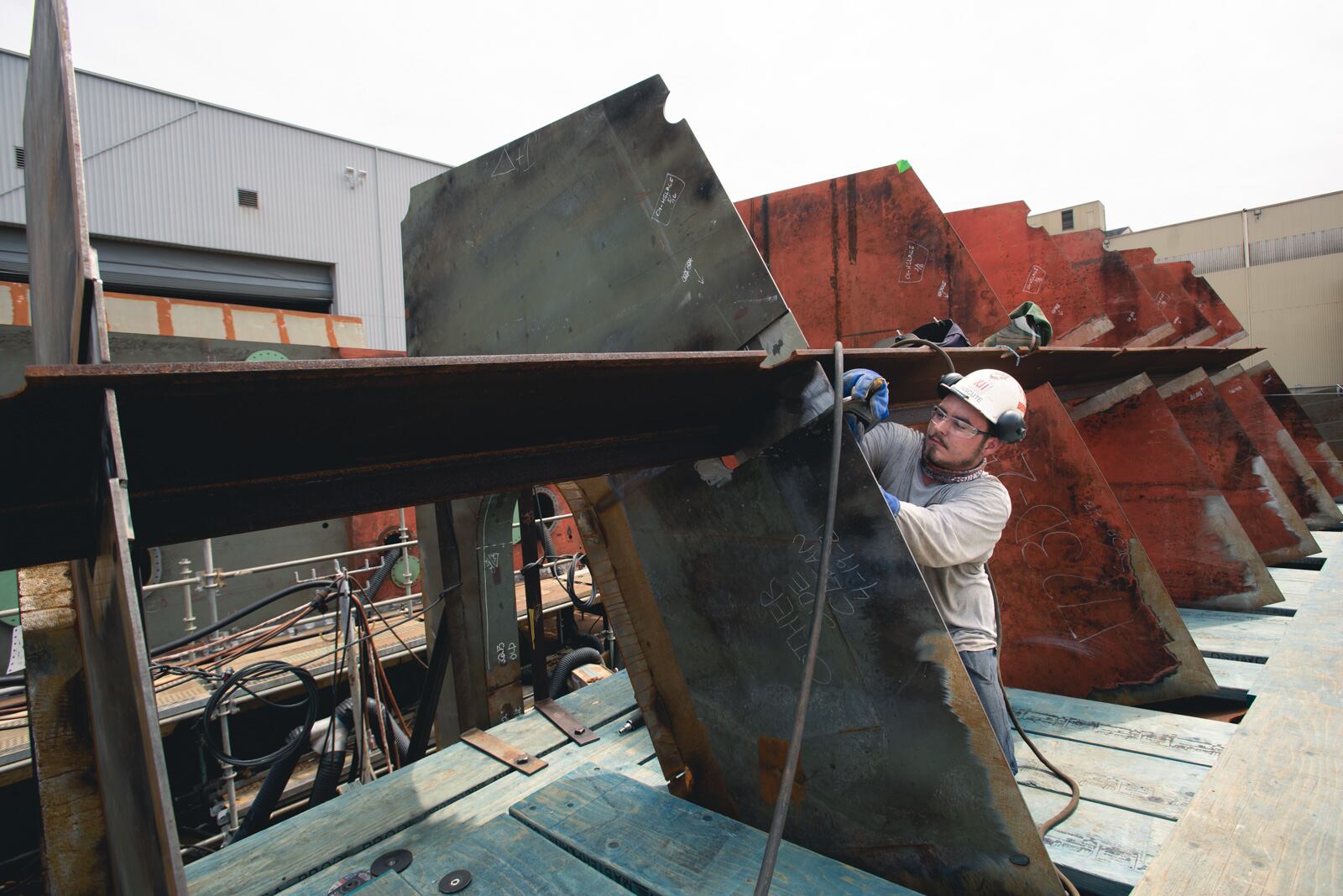
Fields also noted the Ford class was designed in a digital 3D environment, rather than using traditional blueprint drawings. The associated step-by-step digital work instructions weren’t ready for the first two ships, so Ford and Kennedy were built by craftspeople using paper drawings derived from the digital plans — though Kennedy was used to experiment with early digital work instructions and get employee feedback.
Starting with Enterprise, workers at the shipyard used laptops with digital work instructions for each step, with 3D images that can be enlarged and rotated.
“It provides the mechanics a lot clearer picture of what they’re expected to be doing. It helps with first-time quality. It helps the younger craftspeople, who sometimes, we find it takes as much time to learn to read drawings as it does to develop the craft skills,” Fields said.
Enterprise and Doris Miller will be fully built with these digital work instructions, in a first for the Navy.
Fields said the Navy invested significantly in getting the 3D product model and the digital work instructions right, as they will be the basis of not only construction of carriers and submarines at Newport News but also for lifecycle maintenance work at the Navy’s four public shipyards.
Fields said Newport News Shipbuilding made a “generational investment” in buying laptops for all hourly workers so they could access the digital work instructions. But, he said, the investment is yielding other benefits, giving workers immediate access to resources like procedures, troubleshooting manuals and more, as well as better access to their supervisors.
These same tools and processes will be used to build the Columbia-class ballistic missile submarine and the SSN(X) next-generation attack submarine. Future ship classes will all join this same digital environment, Fields said.
Megan Eckstein is the naval warfare reporter at Defense News. She has covered military news since 2009, with a focus on U.S. Navy and Marine Corps operations, acquisition programs and budgets. She has reported from four geographic fleets and is happiest when she’s filing stories from a ship. Megan is a University of Maryland alumna.