3-D printed parts have been used in Navy aircraft for years, but they’ve been mostly structural, not the critical safety parts that could mean the difference between flying and crashing.
That was until Friday, when Naval Air Systems Command held its first flight demonstration of an aircraft — a MV-22 Osprey — with a 3-D printed, metal link and fitting assembly for the engine housing.
"The flight went great," said MV-22 pilot Marine Maj. Travis Stephenson said in a Navy release. "I never would have known that we had anything different onboard."
While it's an Air Force and Marine Corps vertical-lift aircraft now, the Navy has tapped the Osprey as its next carrier on-board delivery vehicle in the 2020s.
The military has dabbled in 3-D printing since the early 1990s, making plastic aircraft flight deck tabletop models and plastic models of medical tools. Critical parts are a new addition.
The process, also known as additive manufacturing, uses plastic, metal or other materials to fashionbuild objects from detailed plans uploaded to a computer. With more facilities and better designs and technology, it could one day allow maintainers to quickly build their own parts rather than having to rely on the parts inventory in the supply system.
The service owns some of its own printers, but, NAVAIR's boss said in the release, in the future will probably contract for a lot of its 3-D printing needs.
"Where I believe we can 'lead' industry is in the development of the AM 'digital thread,' from initial design tools all the way to the flight line — securely maintained and managed through the life of an aircraft program," Vice Adm. Paul Grosklags said.
The parts in the recent test were printed at Naval Air Warfare Center Aircraft Division at Joint Base McGuire-Dix-Lakehurst, New Jersey, where the Navy has worked with Penn State Applied Research Laboratory to make non-critical Osprey parts.
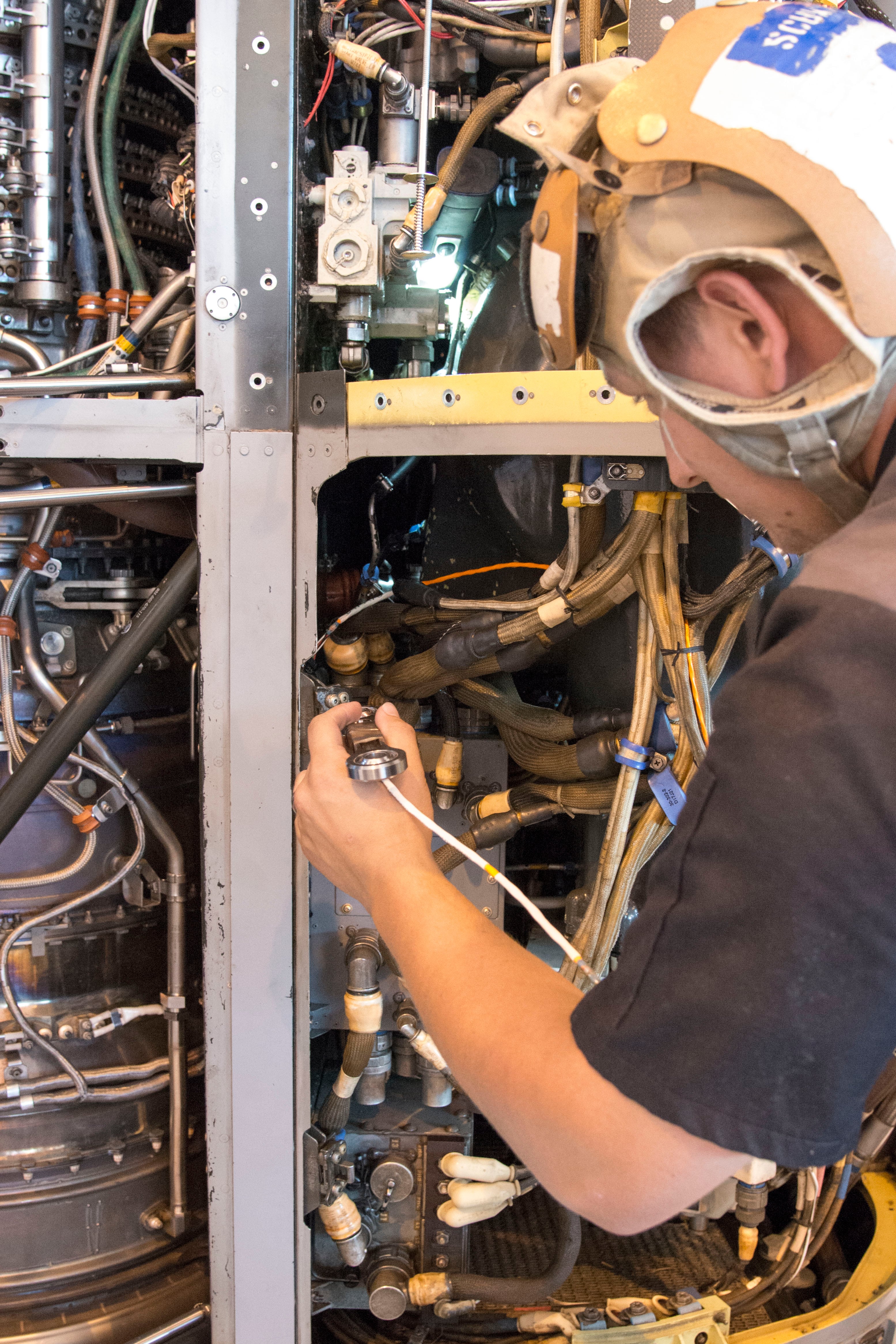
Aviation Mechanic Cody Schwarz works to install a 3-D printed titanium link and fitting on an MV-22B Osprey engine nacelle the day before the flight demonstration.
Photo Credit: U.S. Navy
"The flight today is a great first step toward using AM wherever and whenever we need to. It will revolutionize how we repair our aircraft and develop and field new capabilities — AM is a game changer," said Liz McMichael, AM integrated product team lead, in the release.
Over the past year and a half, she added, her team has made major progress in printing critical parts, and there are plans to use the parts on any Osprey.
"Navy officials envision a future where all parts can be made on-demand globally by fleet maintainers and operators, and our industry partners — stocking digital data instead of ordering, stocking and shipping parts," according to the release.
McMichael and her team have plans to build six more safety-critical parts for the Osprey as well as the H-1 Huey and the CH-53K King Stallion helicopters.
Meghann Myers is the Pentagon bureau chief at Military Times. She covers operations, policy, personnel, leadership and other issues affecting service members.